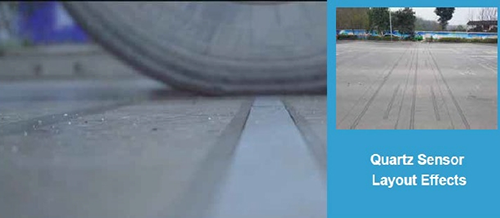
1. Background Technology
Currently, WIM systems based on piezoelectric quartz weighing sensors are widely used in projects such as overload monitoring for bridges and culverts, non-site overload enforcement for highway freight vehicles, and technological overload control. However, to ensure accuracy and service life, such projects require cement concrete pavement reconstruction for the piezoelectric quartz weighing sensor installation area with the current technology level. But in some application environments, such as bridge decks or urban trunk roads with heavy traffic pressure (where the cement curing time is too long, making long-term road closures difficult), such projects are difficult to implement.
The reason piezoelectric quartz weighing sensors cannot be directly installed on flexible pavement is: As shown in Figure 1, when the wheel (especially under heavy load) travels on the flexible pavement, the road surface will have a relatively large subsidence. However, when reaching the rigid piezoelectric quartz weighing sensor area, the subsidence characteristics of the sensor and the pavement interface area are different. Moreover, the rigid weighing sensor has no horizontal adhesion, causing the weighing sensor to quickly break and separate from the pavement.
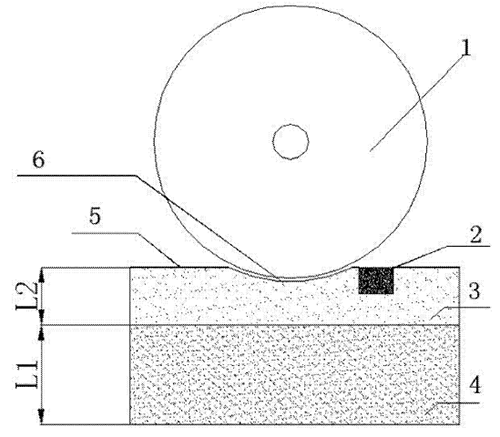
(1-wheel, 2-weighing sensor, 3-soft base layer, 4-rigid base layer, 5-flexible pavement, 6-subsidence area, 7-foam pad)
Due to the different subsidence characteristics and different pavement friction coefficients, vehicles passing through the piezoelectric quartz weighing sensor experience severe vibrations, significantly affecting the overall weighing accuracy. After long-term vehicle compression, the site is prone to damage and cracking, leading to sensor damage.
2. Current Solution in This Field: Cement Concrete Pavement Reconstruction
Due to the problem of piezoelectric quartz weighing sensors being unable to be directly installed on asphalt pavement, the prevalent measure adopted in the industry is cement concrete pavement reconstruction for the piezoelectric quartz weighing sensor installation area. The general reconstruction length is 6-24 meters, with a width equal to the road width.
Although the cement concrete pavement reconstruction meets the strength requirements for installing piezoelectric quartz weighing sensors and ensures service life, several issues severely constrain its widespread promotion, specifically:
1) Extensive cement hardening reconstruction of the original pavement requires a substantial amount of construction costs.
2) Cement concrete reconstruction requires an extremely long construction time. The curing period for cement pavement alone needs 28 days (standard requirement), undoubtedly causing a significant impact on traffic organization. Especially in some cases where WIM systems are necessary but the on-site traffic flow is extremely high, project construction is often difficult.
3) Destruction of the original road structure, affecting appearance.
4) Sudden changes in friction coefficients can cause skidding phenomena, especially in rainy conditions, which can easily lead to accidents.
5) Changes in road structure cause vehicle vibrations, which affect weighing accuracy to a certain extent.
6) Cement concrete reconstruction cannot be implemented on some specific roads, such as elevated bridges.
7) Currently, in the field of road traffic, the trend is from white to black (converting cement pavement to asphalt pavement). The current solution is from black to white, which is inconsistent with relevant requirements, and construction units are often resistant.
3. Improved Installation Scheme Content
The purpose of this scheme is to solve the deficiency of piezoelectric quartz weighing sensors being unable to be directly installed on asphalt concrete pavement.
This scheme directly places the piezoelectric quartz weighing sensor on the rigid base layer, avoiding the long-term incompatibility issue caused by the direct embedding of the rigid sensor structure into the flexible pavement. This greatly extends the service life and ensures that weighing accuracy is not affected.
Moreover, there is no need to perform cement concrete pavement reconstruction on the original asphalt pavement, saving a significant amount of construction costs and greatly shortening the construction period, providing feasibility for large-scale promotion.
Figure 2 is a schematic diagram of the structure with the piezoelectric quartz weighing sensor placed on the soft base layer.
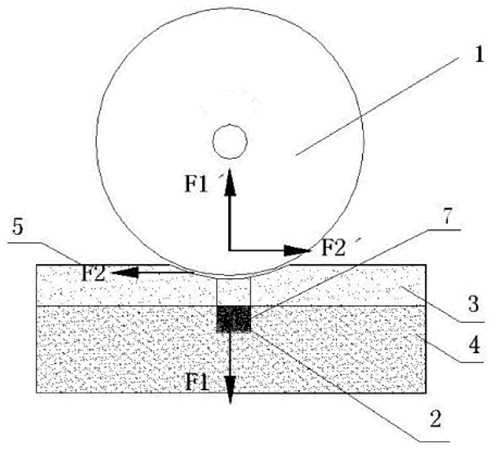
(1-wheel, 2-weighing sensor, 3-soft base layer, 4-rigid base layer, 5-flexible pavement, 6-subsidence area, 7-foam pad)
4. Key Technologies:
1) Pretreatment excavation of the base structure to create a reconstruction slot, with a slot depth of 24-58 cm.
2) Leveling the bottom of the slot and pouring filler material. A fixed ratio of quartz sand + stainless steel sand epoxy resin is poured into the bottom of the slot, evenly filled, with a filler depth of 2-6 cm and leveled.
3) Pouring the rigid base layer and installing the weighing sensor. Pour the rigid base layer and embed the weighing sensor into it, using a foam pad (0.8-1.2 mm) to separate the sides of the weighing sensor from the rigid base layer. After the rigid base layer solidifies, use a grinder to grind the weighing sensor and the rigid base layer to the same plane. The rigid base layer can be a rigid, semi-rigid, or composite base layer.
4) Casting of the surface layer. Use material consistent with the flexible base layer to pour and fill the remaining height of the slot. During the pouring process, use a small compaction machine to slowly compact, ensuring the overall level of the reconstructed surface with other road surfaces. The flexible base layer is a medium-fine granular asphalt surface layer.
5) The thickness ratio of the rigid base layer to the flexible base layer is 20-40:4-18.
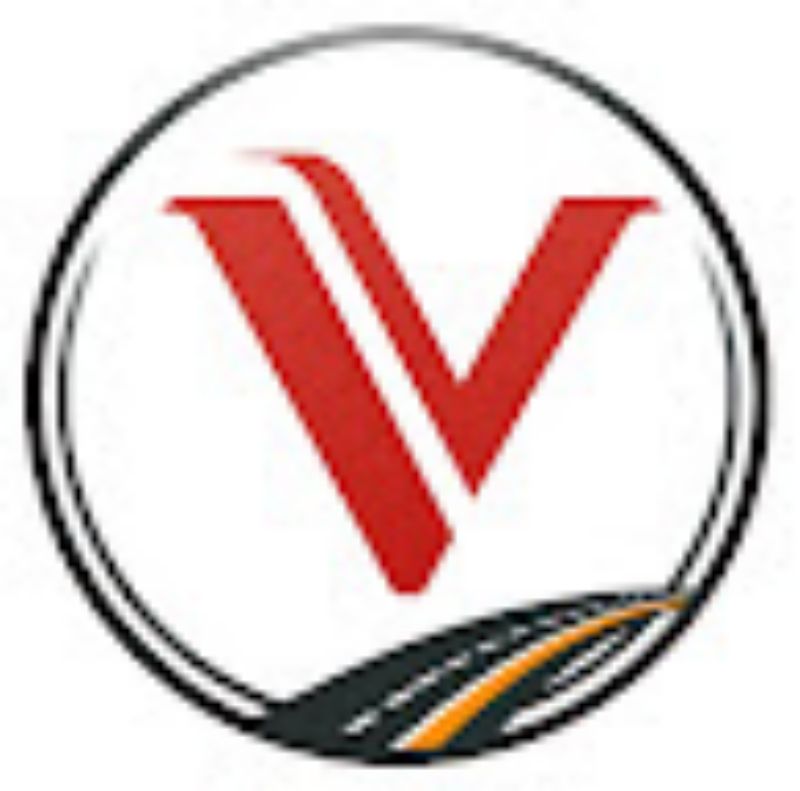
Enviko Technology Co.,Ltd
E-mail: info@enviko-tech.com
https://www.envikotech.com
Chengdu Office: No. 2004, Unit 1, Building 2, No. 158, Tianfu 4th Street, Hi-tech Zone, Chengdu
Hong Kong Office: 8F, Cheung Wang Building, 251 San Wui Street, Hong Kong
Factory: Building 36, Jinjialin Industrial Zone, Mianyang City, Sichuan Province
Post time: Apr-08-2024